Metalli 3D-printimine: detailid vastavalt soovile – kas see on utoopia?
Elame muutlikul ajal. Energiarevolutsioon, geopoliitilised pinged ja ebakindlad tarneahelad panevad meid kõiki pidevalt proovile. Arvamused on sageli vastukäivad ja arutelud tulised. Üks on aga kindel: tootmine on keerulisem kui kunagi varem – tulevikus peab see ressursitõhusam, kiirem, paindlikum, kuluefektiivsem, keskkonnasõbralikum ja võimalikult väikeste partiidena olema. Siin tulebki appi metalli 3D-printimine.
Metalli 3D-printimine: mis see täpselt on?
Metalli 3D-printimine, nagu ka kõik teised 3D-printimise protsessid, on tootmisprotsess, mis on paljude toodete tootmist nii tehniliselt kui ka majanduslikult muutnud. Toote kiht-kihilt ehitamine, mis eile tundus ulmena, on täna reaalsus. Kolmemõõtmelised objektid saadakse materjali kihtlisandustehnoloogiaga. 3D-printimine kogub nüüd üha rohkemates tööstusharudes populaarsust, kuna see suurendab ettevõtete paindlikkust ja seega ka konkurentsivõimet. Potentsiaalseid rakendusi võib leida autotööstuses, elektroonikas ja tööriistade valmistamisel, nafta- ja gaasitööstuses, lennunduses, elektrijaamade ehituses, meditsiinitehnoloogias ja ehitustööstuses.
Metalli 3D-printimine pakub tohutut potentsiaali ja mitmeid eeliseid
Klassikalised tootmistehnikad nõuavad sageli keerukate vormide ja tööriistade ehitamist ning on seotud pikkade teostusaegade ja kõrgete seadistamiskuludega. Kihtlisandustehnoloogiaga tootmine aitab drastiliselt arendustsükleid lühendada. „Nõudmisel” komponentide printimine kiirendab prototüübi ehitamist (kiire prototüüpimine), võimaldab tootmist õigel ajal – kaotades varuosade laoseisu ja sellega kaasnevad kulud – ning lihtsustab oluliselt remonditööd. Kui on vaja varuosi, valitakse tarkvarast välja õiged „retseptid” ja prinditakse või kopeeritakse vastavalt vajadusele. Komponentide geomeetriale pole peaaegu mingeid piiranguid. Valmistada saab isegi keerulisi kärg- ja õõneskonstruktsioone. Metalli 3D-printimine pakub prototüüpide ehitamisel erilise eelise, kuna disainiprobleeme saab varakult avastada ja ilma keerukate ning kulukate vormide ja kinnitusdetailide tootmiseta lahendada. Samal ajal kiirendab protsess innovatsiooni ja tõstab ettevõtte tootlikkust. Prinditud komponendid, mis on kuju ja koormuse poolest optimeeritud (topoloogiaga optimeeritud), on sageli kergemad, kui tavalised, ja võivad lennukite või sõidukite kütusekulu vähendada, suurendades samal ajal ka transpordivahendite kasulikku kandevõimet.
Metalli 3D-printimine tipptasemel keevitustehnoloogiaga
3D-printimise protsesside jaoks on saadaval erinevad kihtlisandusmeetodid. Objekte ehitatakse ja kujundatakse kiht-kihi haaval, ühendades üksikud materjalikihid. Metalli 3D-printimisega seotud protsessid jagunevad kahte põhitüüpi: pulbripõhine ja traadipõhine. Pulbripõhiste protsesside puhul ehitatakse kihid üles sulametallipulbri abil. Kõige tavalisem meetod, pulberkihtprotsess, on suure täpsusega, kuid suhteliselt aeglane. Traadil põhinev protsess ehitab tooriku üles sulatades traadi kas elektronkiire, laseri või kaare abil. Nendel protsessidel on kõrge protsessikiirus ja seepärast aitavad need tootmisaega lühendada. Traatelektroodi otsesulatamine või lühidalt DED-Arc on keevituskaarel põhinev protsess, mis kasutab gaas-metallkaarkeevitus protsessi (GMAW). Antud metalli 3D-printimise variandi tootlikkus on kuni 4 kg/h, kuid see peaks tulevikus suurenema, kuna kasutusele võetakse eriprotsessid ja mitme traadi lahendused. Trükiprotsessi valikul on olulised tegurid seadme- ja materjalikulu. DED-Arc meetodi keskmes on stabiilne keevitussüsteem. Pole vaja kulukaid vaakumkambreid nagu näiteks elektronkiire protsessis. „Õige keevituse trajektoor koos õigete keevitusparameetrite ja -protsessi väärtustega on hea trükitulemuse jaoks ülioluline,” selgitab WAAM tootmise ekspert Philipp Roithinger. „Lisaks on vaja automatiseeritud keevitussüsteemi, mis tagab, et keevituspõleti järgib täpselt rada. Kvaliteetsed keevitusrobotid pakuvad tänapäeval koguni +/- 0,02 mm positsiooni- ja kordustäpsust.”
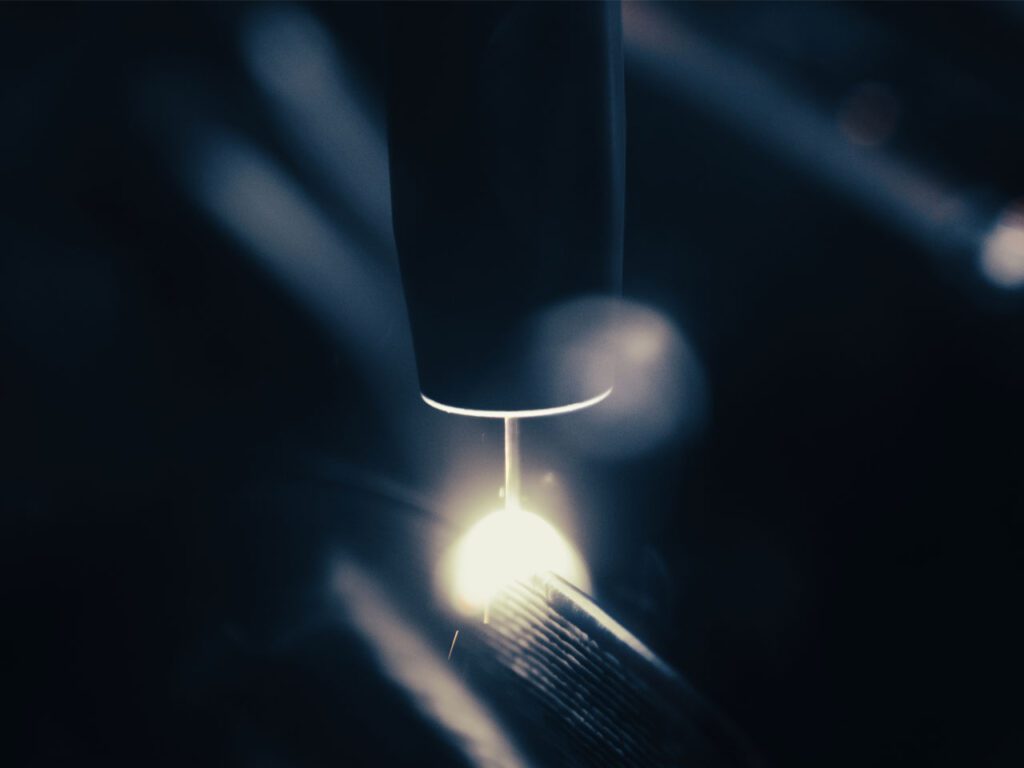
Komponentide tootmine suure mahuga metalli 3D-printimise abil
Kasutatava keevitusprotsessi stabiilsus ja temperatuuri juhtimine on DED-Arc jaoks olulised. Protsess peab olema madala soojussisestusega, st võimalikult „külm”, et komponenti ei pääseks liiga palju energiat. Keevitatud kihid peaksid samuti võrdse kvaliteediga olema, pritsmevabad ja ühtlased. Kui protsessis on viga, siis kordub see igas järgmises kihis. Ainulaadne Cold Metal Transfer (CMT) kaarkeevitusprotsess oma intelligentsete protsessijuhtimise variantidega vastab juba iseenesest nendele nõudmistele, mida kihtlisandustehnoloogiale esitame. „CMT-d iseloomustab äärmiselt stabiilne kaar ja see võimaldab paindlikku soojussisestust,” selgitab Roithinger ja lisab: „Protsess võimaldab peaaegu pritsmevaba materjali ülekannet, mis aitab vigu vältida ja järeltöötlust vähendada. Lisaks võimaldab CMT suurepäraseid sulatuskiirusi saavutada ja iga tilga eraldumist kontrollida, et saaksime veelgi täpsemalt töötada. Veelgi enam, oleme CMT Additive Pro-ga täiendavalt optimeerinud 3D-printimise protsessi, et tagada ühtlasem kihi struktuur ja parem soojussisestuse kontroll.”
Kaare pidev jälgimine metalli 3D-printimisega
Vaatamata kõrgtehnoloogilisele seadmestikule on soovitatav kaarel ja tilkade eraldumisel pidevalt silma peal hoida. Spetsiaalseid kaamerasüsteeme saab kasutada keevitustööde jälgimiseks ja võimalike vigade tuvastamiseks nii, et keevitaja saaks vajadusel kiiresti tegutseda. Näiteks ArcView 2 on protsessispetsiifiline kaamerasüsteem, mis võimaldab keevitust otse töökabinetist jälgida. Kaamera annab teravaid pilte millisekundi vahemikus. Üksikud fotod tehakse lühise faasis, st täpselt sel hetkel, kui kaar puudub. See pakub keevitusspetsialistidele protsessi juhtimiseks täiuslikku reaalajas videot. Seda saab vaadata ekraanilt väljaspool roboti tööala, tagades keevitajatele parima kaitse kaarekiirguse eest.
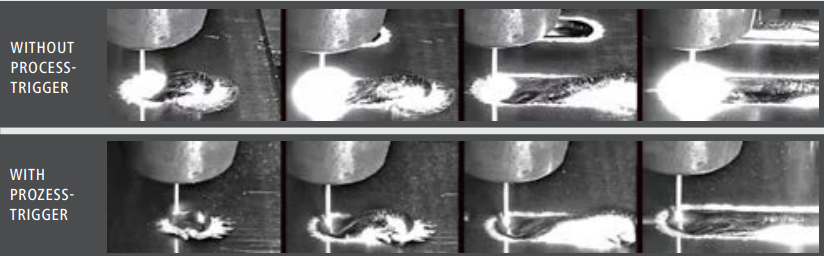
Majanduslikult efektiivne ja keskkonnasõbralik
Kihtlisandustehnoloogiaga tootmise alternatiivid oleksid freesimine või mehaaniline töötlemine, kuid need tekitavad palju jäätmeid, kuna vajalikud osad lõigatakse metallplokkidest välja – sageli tohututes mastaapides. Õõneskehaga töötades on jäätmete hulk väga suur. Lisandtootmise korral toodame komponente kihtide kaupa, nii et pärast on vaja ainult viimistleda. Lisaks pole seegi alati nõutav. Seetõttu on materjalikasutus tavapäraste tootmismeetoditega võrreldes palju väiksem. Olukordades, kus 80% materjalist kaob teatud kehade freesimise käigus, on selle ekvivalent lisandite valmistamisel – näiteks DED-Arc’i puhul – sageli vaid 20%, kusjuures kadu tekib vaid järeltöötlemisel. „Vaatame markantset näidet: allpool näidatud metallist sõukruvi valmistati metalli 3D-printimisega. Kui see oleks freesitud plokist, oleks plokk olnud 60x90x90 cm suurune ja kaaluks umbes 4 tonni, samas kui valmis komponent kaalub veidi alla 100 kg,” räägib Roithinger.
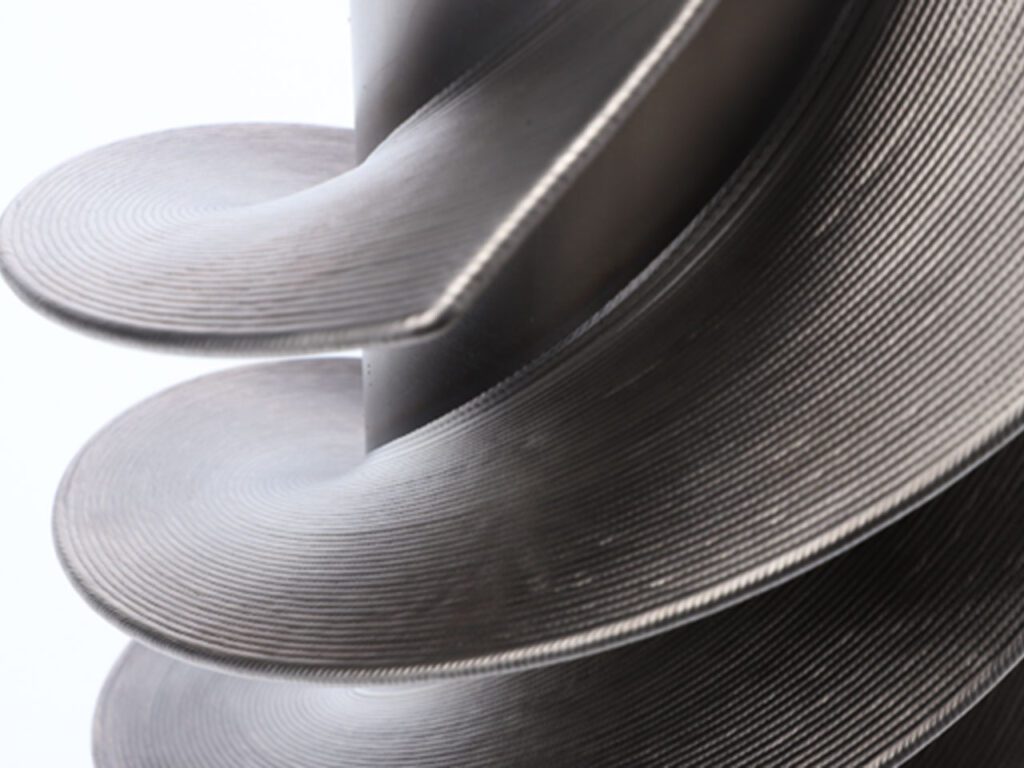
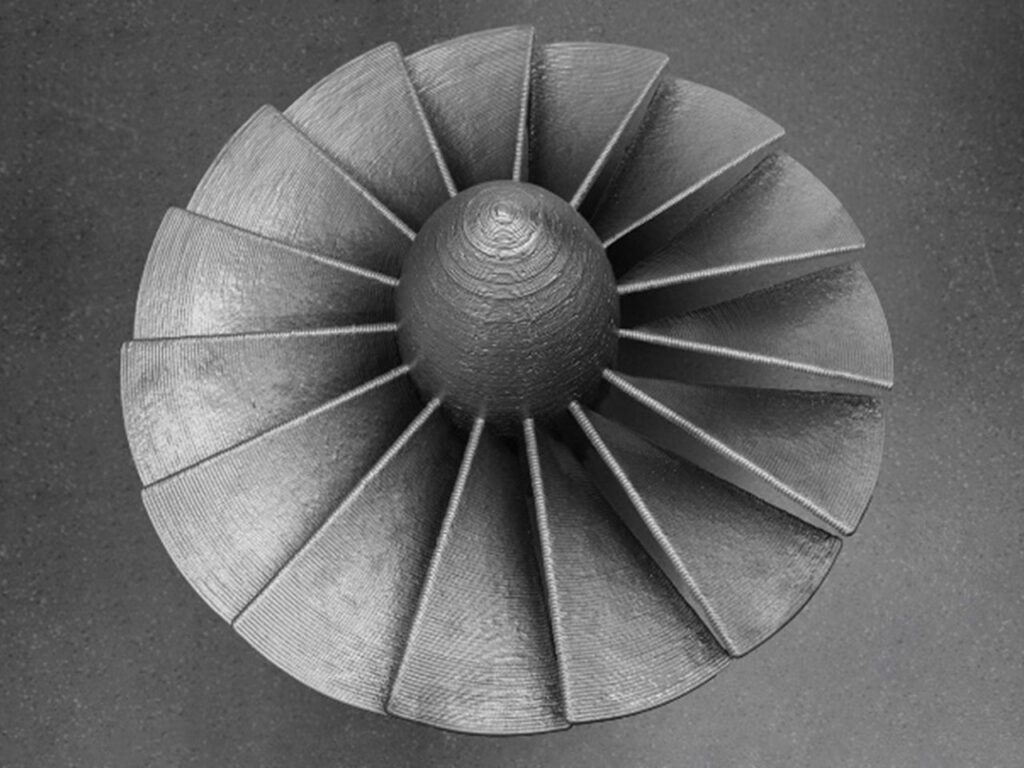
Metallist 3D-printimise tulevik Froniuses – millised on tuleviku väljavaated?
„Kihtlisandustootmisel on tohutu potentsiaal. Nagu uute tehnoloogiate turule tulekul omane, on tavaline esmane vastuseis, enne, kui sobivad rakendused leitakse ja tehnoloogia õitsema hakkab. DED-Arc on teiste 3D-meetoditega võrreldes veel noor,” selgitab Roithinger. Samas on juba praegu tohutu nõudlus kahjustatud osade rekonstrueerimise ja remondi järele. Metallist 3D-printimine võimaldab meil pikendada komponentide nagu sõukruvi või kruvikonveieri kasutusiga aastate võrra. Kuid mitte ainult: kõiki varuosi, mida võib vaja minna, saab soovi korral printida. Paljud kaubandus- ja tööstusettevõtted muutuvad asukohast ja tarneajast sõltumatuks, mis muudab nad konkurentsivõimelisemaks – ja see on otsustava tähtsusega. Samuti säästavad nad tarbetuid ladustamiskulusid. Froniuse insenerid viivad lisandprotsessi uuele tasemele, et metalli 3D-printimise võimalike rakenduste valikut suurendada ja veelgi suurem protsessi stabiilsus saavutada. „Meie visioon on, et varem või hiljem hakkame kohe pärast projekteerimisfaasi printima ja 3D-printer sülitab välja ideaalse tulemuse. Kui see tehnoloogia on loodud, oleks võimalik komponentide asemel lihtsalt toote digitaalset „retsepti” levitada. See sisaldaks siis nõutavaid printimisjuhiseid koos keevitusjuhise, keevitusparameetrite, pausi aegade ja kõige muuga, mida kasutaja vajab. Kliendid peavad selle retsepti vaid automatiseeritud keevitussüsteemi arvutisse üles laadima ja vajutama nuppu „Prindi”, “ lisab Roithinger, andes Froniuse innovatsioonimeeskonna mõtetest kokkuvõtva ülevaate.