Rauataltsutajad 2. hooaeg osa 5: Scanweld
Rauataltsutajate viiendas osas võeti mõõtu torukeevituse keerulises maailmas Scanweldi tehases Jõelähtmel. Võistlustulle asusid kolm kanget keevitajat: Kristjan, Silvein ja Roman, kelle ülesandeks oli valmis keevitada torukoost ehk spool. Tegemist oli keerulise ülesandega, sest töö peab olema täpne ja korrektne. Lisaks pidi valmis spool olema täiesti lekke- ja survekindel.
Vaata 5. osa: Rauataltsutajad | ETV | ERR
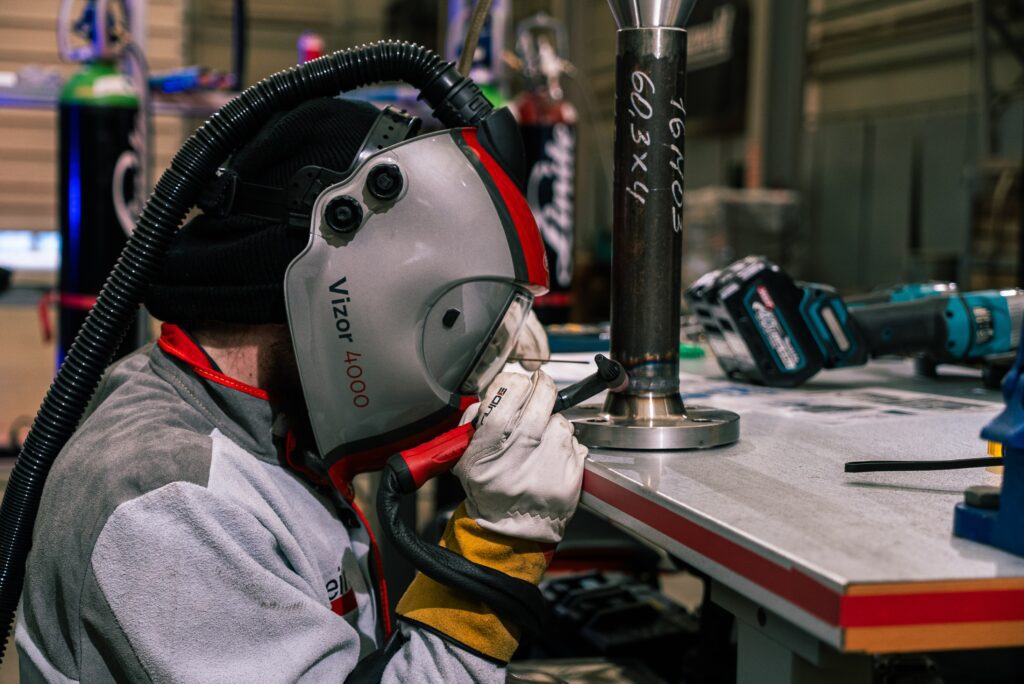
Survekindlust keevisliidetes tagasid töökindlad ja kompaktsed Fronius TransTig 170 vooluallikad ja keevisvannist eralduva kiirguse ning osakeste eest kaitsesid Optrel Crystal 2.0, Vegaview 2.5 ja Fronius Vizor 4000 filtersüsteemiga keevitusmaskid.
TIG keevituse ajaloost
TIG-keevituse lõi 1940. aastatel keevitaja nimega Russell Meredith, kes töötas Northrop Aircraft Corporationis Lõuna-Californias. Ta lõi selle tehnika, kuna tolleaegsed meetodid olid alumiiniumi- ja magneesiumisulamite keevisõmbluste jaoks ebapiisavad. See oli tohutu edu ja andis Ameerika tööstusele võimaluse laevu, lennukeid ja muid tooteid kiiremini kui kunagi varem ehitada. President Roosevelt kiitles selle protsessi üle isegi kirjas Winston Churchillile.
Protsessi patendi ostis Union Carbide’i Linde osakond ning ettevõte töötas välja ja müüs selle tehnika jaoks erinevaid põletid, osi ja kulumaterjale kuni 1960. ja 1970. aastateni, mil nende protsessi ja TIG-iga seotud tööriistade patendid aegusid. Linde protsess kasutasid heeliumi. Mitmed ettevõtted alustasid TIG-põletite ja tarvikute turustamist, kuid juhtiv oli CK Worldwide, Seattle’is asuv ettevõte, mis tegi tihedat koostööd kosmosehiiglasega Boeing. CK lahendas oma toodete väljatöötamisel mitmeid rakendusprobleeme ning nende põletid, gaasisäästmiskomplektid ja volframilihvijad said paljude lennukite tootmisega seotud isikute valikuks.
Teine tööstuse liider Linde-järgsel ajastul oli Weldcraft. Lõuna-Californias asuv ettevõte on spetsialiseerunud selliste põletite remondile, mille olid vanarauaks saatnud mitmed ettevõtted, sealhulgas Hughes ja Rockwell. Keevitustehnikud põletasid pidevalt põletite plastkatte maha, et kahjustatud volframile ligi pääseda. Seejärel tehti remont ja põleti suleti uuesti ränipõhisesse materjali. Tulemuseks oli uut ja töökindlamat tüüpi tööriist, mis läks väiksema tõenäosusega rikki.
TIG-keevitusmasina ajalugu
Esimesed TIG-keevitusmasinad töötas välja Linde, kui neile kuulus TIG-protsessi patent. Need masinad kaalusid sadu kilosid, kuid masinad muutusid aja jooksul väiksemaks. 1970. aastatel võttis Miller Corporation kasutusele ruudukujulise lainekuju funktsiooni, mis võimaldas keevitusmasinaga töötades voolutugevust paremini juhtida. Trükkplaadid olid valdkonna järgmine suur areng ja andsid TIG-keevitajale võimaluse veelgi täpsemaid seadistusi teha.
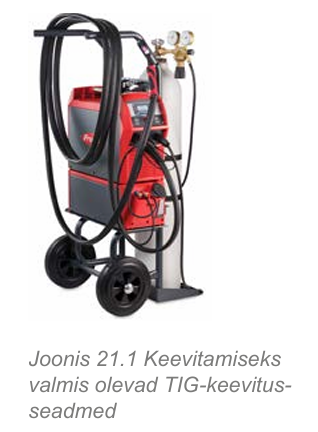
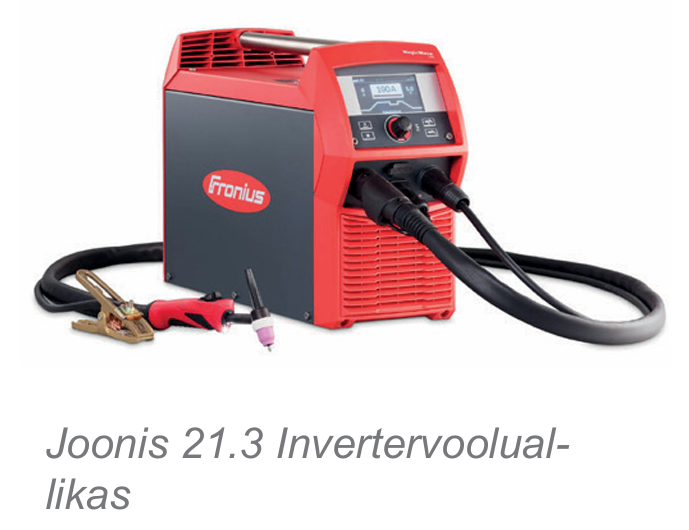
Mis on TIG-keevitus ja kuidas see töötab?
Volfram-inertgaasi (TIG) keevitamine on kaarkeevitus. Nagu ka teiste kaarkeevitusviiside puhul, on põhiprintsiip see, et elektroodi ja keevisõmbluses sulavate metallide vahele elektrikaare tekitamiseks kasutatakse elektritoiteallikat. Mittesulav elektrood on valmistatud haruldasest metallist volframist ning seda jahutatakse ja kaitstakse inertgaasiga, tavaliselt argooniga. TIG-keevitaja hoiab ühes käes metallpõletit, teises aga täitematerjali kaare söötmiseks. Protsessi kasutatakse alumiiniumi, roostevaba terase ja muude materjalide täpsete keevisõmbluste jaoks; metallide ülekuumenemise vältimiseks saab kaare voolutugevust juhtida nii puldiga kui põletist kas jala- või sõrmeotsaga.
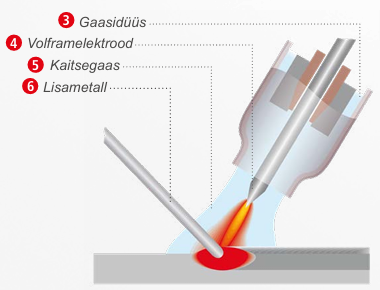
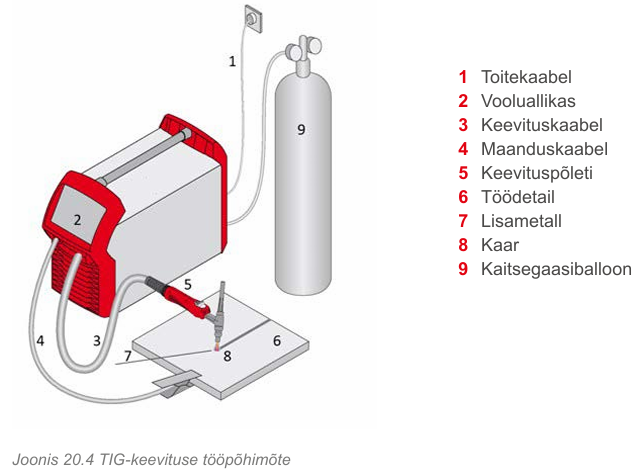
TIG-keevituse tulevik
Selle tehnika ja TIG-keevitusmasina arendused olid Ameerika tööstuse peamised saavutused alates II maailmasõjast kuni tänapäevani. Protsessi ja selle tööriistu täiustatakse senimaani ning ka tulevikus.
Olulised asutajad
TIG-keevituse ajalugu algab 1890. aastal, kui C. J. Coffin saab patendi mitteoksüdeerivas gaasis keevitamiseks. Elektroodina kasutas ta süsinikvarrast. Volframelektroode veel ei eksisteerinud. 1926. aastal arendas seda protsessi edasi H. M. Hobart. Ta kasutas oma katsetes heeliumi. Samal aastal uuris P. K. Devers ka TIG-protsessi, kuid ta kasutas oma katsetes argooni. Ja nii juhtuski, et põhimõtteliselt sama protsessi jaoks tekkisid kaks nime, Heliarc ja Argonarc. Läks 1941. aastani, enne kui Russel Meredithile alumiiniumi ja magneesiumi keevitamiseks patent anti. Russel Meredith töötas ettevõttes Northrop Aircraft. Teise maailmasõja ajal oli surve sõjatööstusele suurem ja ennekõike tootmiskiirusele. Northrop Aircraftis keevitati esimesed lennukite alumiiniumist ja magneesiumist osad. Protsess sai seejärel tuntuks kui Heliarc Welding. 1950. aasta alguses müüs Northrop Aircraft protsessi ja nime Heliarc Union Carbide’i Linde divisjonile. Lindel oli protsessi ja põletite arendamiseks palju rohkem võimalusi. Seni kasutati keevitamiseks ainult inertgaasiga täidetud ruume.
Esimesed põletid
Esimesi põleteid oli väga raske kasutada – need olid suured, rasked ja õhkjahutusega. Tasapisi töötati välja põleti sellisel kujul nagu me seda praegu kasutame. 1960. aastal anti Gene Gormanvan Lindele gaasiläätse patent. Ta kasutas omamoodi paagutatud pronksi. Gaasilääts muutis gaasi väljavoolu väga stabiilseks ja see ei keerlenud enam. See oli eriti oluline heeliumi kasutamise puhul. Heelium on palju kergem kui argoon ja seetõttu on seda rohkem vaja. See põhjustab keeriseid ja hapnik võib gaasiga seguneda. Sellisel segamisel on keevitustulemusele negatiivne mõju.
Paagutatud pronksgaaslääts on endiselt parim gaasilääts, kuid selle hinna tõttu kasutatakse seda ainult väga erilistes rakendustes. Aastal 1961, kui protsess nimetati ümber GTAW-ks, Gas Tungsten Arc Welding, anti teisele Linde töötajale Cliff Hillile patent gaasiläätse jaoks, mis põhines üksteise peale paigutatud väga peentel võrkudel. Cliff Hill oli TIG protsessi edasiarendamise jaoks väga oluline. Ta oli esimene, kes töötas välja vesijahutusega põleti. Kuid mitte Linde, vaid kaks Ameerika ettevõtet turustavad Linde-stiilis põleteid kogu maailmas; CK ja Weldcraft. Mõlemad ettevõtted olid lennukitööstusega väga tihedalt seotud.
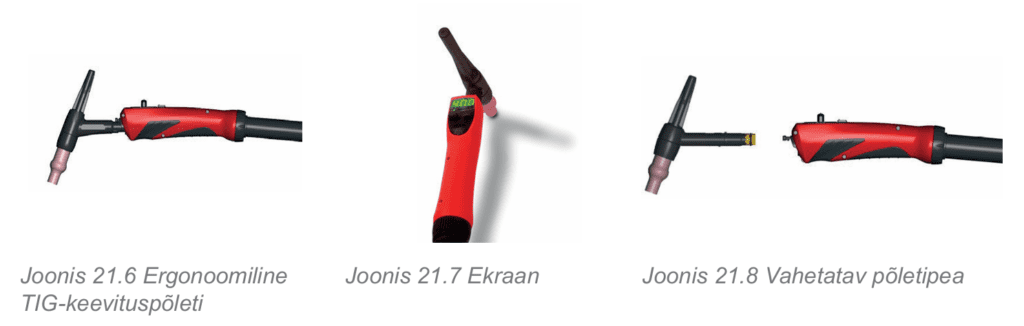
Varustus
Seadmetena kasutati suuri ja raskeid alalditega trafosid. Hea keevitustulemuse saavutamine nendega polnud kaugeltki lihtne. See muutus palju paremaks, kui Miller tuli välja ruutlainevormiga. See muutus veelgi paremaks, kui seadmetesse lisandusid trükkplaadid. Määratavate parameetrite arv muutus järjest suuremaks. Ja alates inverteri kasutuselevõtust on seadistusvõimalused peaaegu lõpmatud.
Protsessi numbrid
IIW, rahvusvaheline keevitusinstituut, nimetas protsessi ümber TIG-iks, Tungsten Inert Gas. TIG protsessi erinevatele võimalustele anti ka numbrid vastavalt standardile EN ISO 4063: 2009.
Kirjeldused
- 141: TIG-keevitus volframelektroodiga inertgaasi keskkonnas täistraadi või vardaga
- 142: TIG-keevitus ilma täitematerjalita
- 143: TIG-keevitus täidistraadi või -vardaga
- 145: TIG-keevitus täistraadi ja redutseeriva gaasiga
- 146: TIG-keevitus täidistraadi ja redutseeriva gaasiga
- 147: TAG-keevitus aktiivgaasi keskkonnas volframelektroodiga
Mõnikord näeb keevitamise nimetust “WIG”. Seda nime leidub peamiselt saksa keelt kõnelevates maades. Saksa keeles on volfram “Wolfram” ja protsessi nimetatakse Wolfram Inert Gas või WIG. Viimastel aastatel on aga protsessi nimetusena kasutatud üha enam sõna TIG. Kogemusega keevitajad räägivad sageli argoonkeevitusest.
Protsessi omadused
Olenemata sellest, kuidas protsessi nimetatakse, on sellel mõned spetsiifilised omadused.
- See on protsess, mille keevismetalli puhtusaste on väga kõrge.
- Protsess on rakendatav kõikide metallide, mustade ja värviliste metallide puhul.
- Protsessi saab väga hästi automatiseerida ja robotiseerida kõikides keevitusasendites täitematerjaliga ja ilma.
Muud piiravad omadused
- See on väga aeglane protsess.
- See on väga kuum suure soojussisestusega protsess.
- Võib esineda suuri deformatsioone, eriti roostevaba terase puhul.
- Protsess on tundlik tuuletõmbele ja seda saab ainult siseruumides kasutada.
Aegluse ja soojussisestuse tõttu võib TIG-protsess mõne materjaliga probleeme tekitada. Eriti roostevaba terasega. Sama soojussisestuse korral deformeerub see materjal viis korda rohkem kui teras. See tähendab, et roostevaba terase keevitamisel tuleb tähelepanelikult vaadata, kuidas keevitada ja kas on parendusvõimalusi. Vasest tugiriba kasutamine võib võimalusel palju soojust eemaldada ja seeläbi liigset deformatsiooni vältida. See säästab palju järeltöötlust.
TIG-keevitus ilma täitematerjalita
TIG-keevitusprotsessi saab läbi viia täitematerjaliga või ilma. Kui täitematerjali ei kasutata ja keevitamine toimub käsitsi, on keevitamine enamasti kosmeetiline ega pea kõrgetele nõuetele vastama. Eelkõige peab see hea välja nägema. Automatiseeritud TIG-keevitusel on võimalik ilma täitematerjalita väga häid keevitustulemusi saavutada.
TIG-keevitus täitematerjaliga
Käsitsi keevitamise korral lisab vardakujulise täitematerjali keevitaja. Nende varraste pikkus on tavaliselt üks meeter ja läbimõõt sõltub valitud voolutugevusest. Tänapäeval on olemas ka põletid, kus traat söödetakse automaatselt poolilt, olgu see külm või kuum. See võib protsessi tõhusust oluliselt parandada. Nende põletite kasutamisel on oma piirangud. Keevitatava detaili ligipääsetavus ei ole alati optimaalne või pole üldse teostatav.
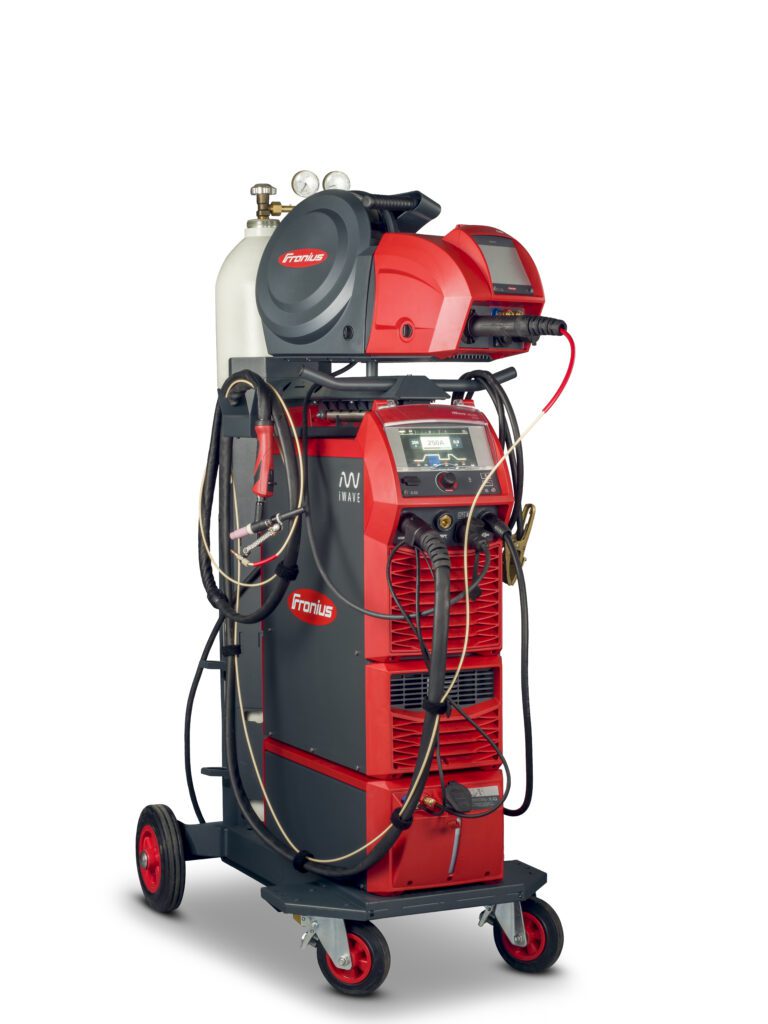
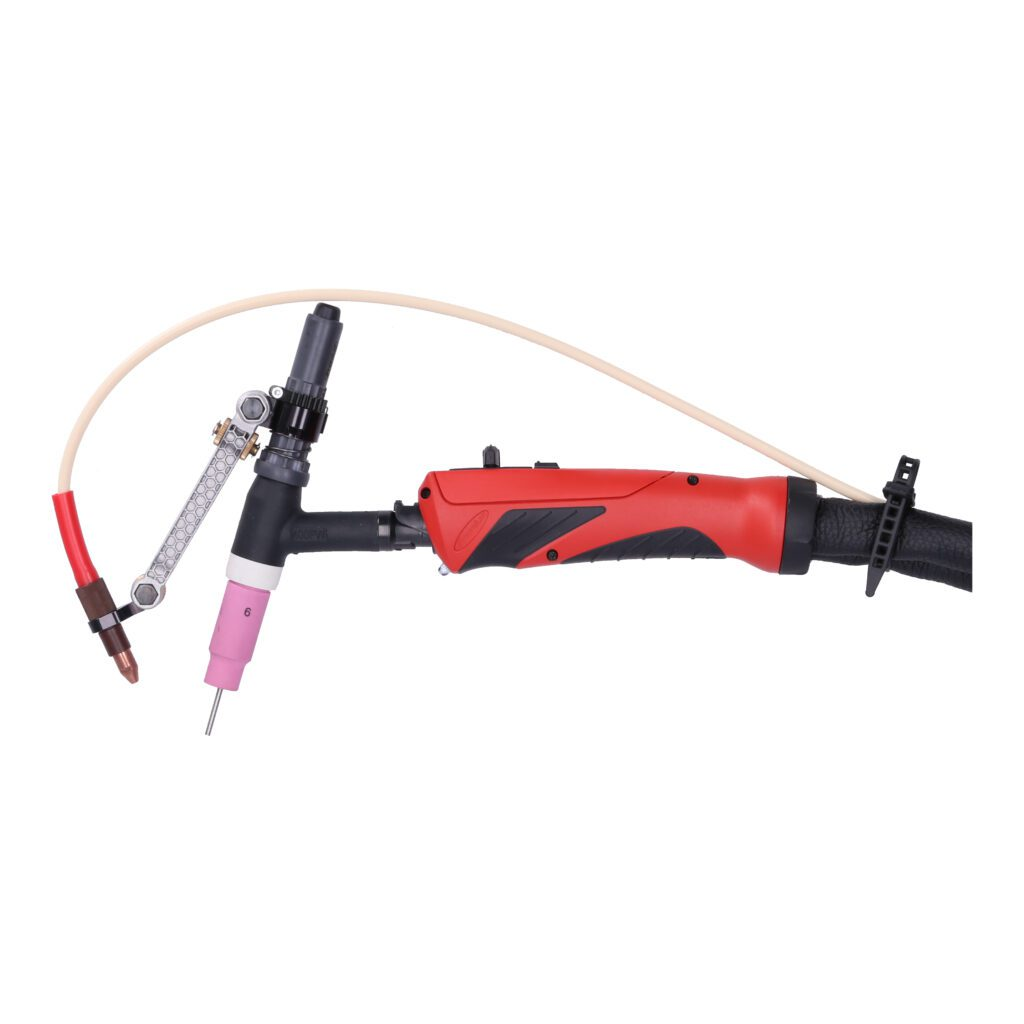